HOP System
Revitalizing forests through houses made of homegrown materials.
In 1997, we established an original housing supply system (HOP), coordinating the entire process, from the procurement of raw wood, lumber, and distribution to design and construction as a collaboration. The method uses drop shipping system featuring onsite timber precutting and drastically reduced the distribution cost. The system is an overall revision of housing from multiple aspects, including building method, performance, design, and distribution.
The concept behind the system was “to revitalize and protect Japanese forests by utilizing them for homebuilding.” In coming up with the concept, our focus was on artificial forests (=forest thinning). Unlike natural forests, artificial forests are nurtured through regular thinning. At that time, however, there were various technical and distributional limitations obstructing the commercial use of artificial forests. Therefore, we realized houses made from artificial forests, which were hitherto considered impossible, through the development of new components fully taking advantages of artificial forests, standardization, and the establishment of a distribution system based on drop shipping.
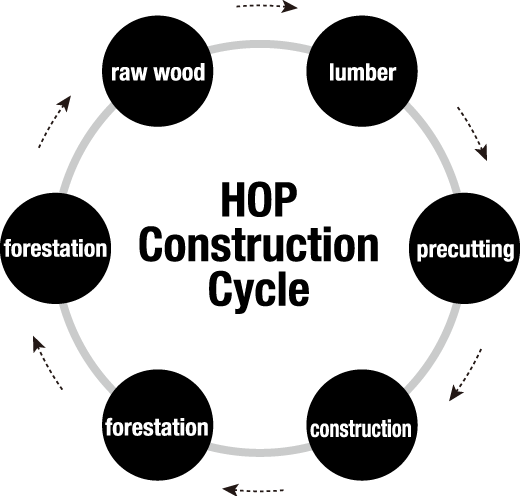
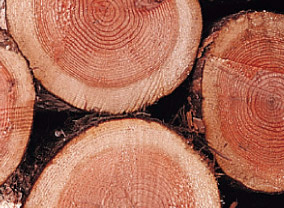
Certified “Sustainable Green Ecosystem” timber
- ●Ecology-forming new forestry
- ●Stable procurement of thinned wood from national,
prefectural, and private forests - ●Environmental Symbiotic House certification
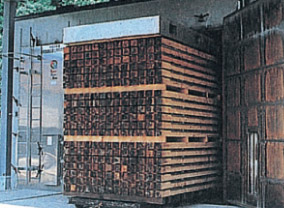
Lumber
HOP Group Ashibetsu Plant
HOP Group Rubeshibe Plant
- ●Lumbering, processing, building materials, furniture & woodcraft materials, optimization of all materials
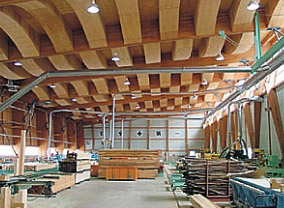
Innovative precutting method
HOP Group Rubeshibe Plant
HOP Group Tomakomai Plant
- ●Development and distribution of innovative production methods and hardware
- ●Advanced use of forest thinning [Hokkaido Forest Products Research Institute]
- ●innovative production method development programs
- ●Standardization of housing components
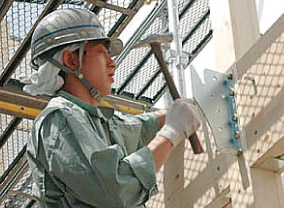
Architecture / Construction through innovative production methods
- ●Provision of healthy houses with extensive amenities
- ●Network-based distribution revolution
- ●Streamlined system enabled by innovative production methods (airtightness, high insulation, high durability)
[Hokkaido Urban Institute of Housing in Cold Region] [Japan Housing and Wood Technology Center]
Logging, drying, and lumbering homegrown timber
SGEC certified forest timber, etc. used for HOP houses are logged in the forests of Hokkaido, collected in the timber basin to be dried naturally, and processed as lumber.

In 1996, HOP jointly founded a cooperative association with lumber producers in Ashibetsu City, Hokkaido and established the drop shipping system.
Lumber used for HOP houses are processed here.
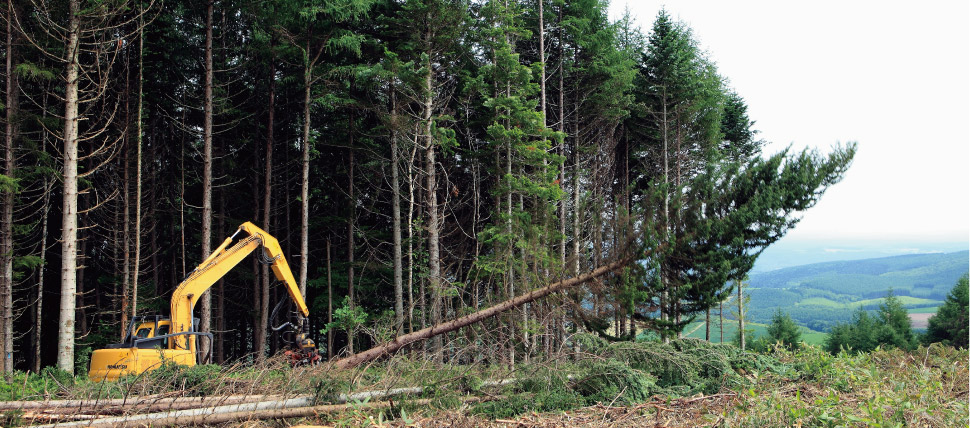
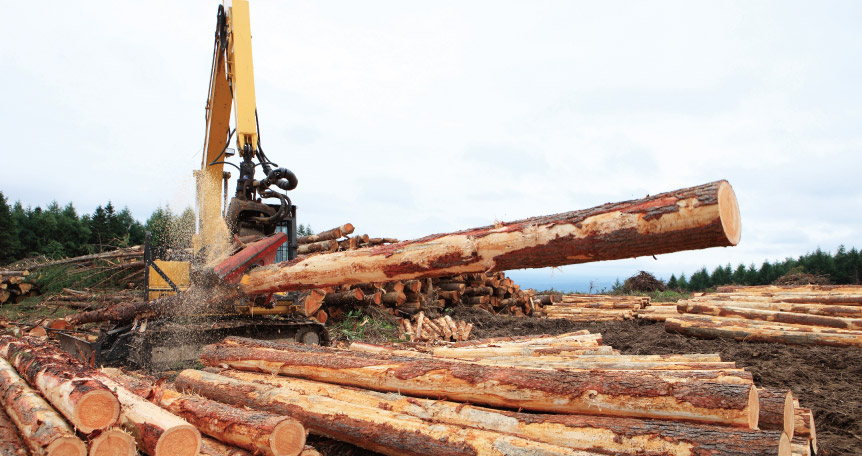
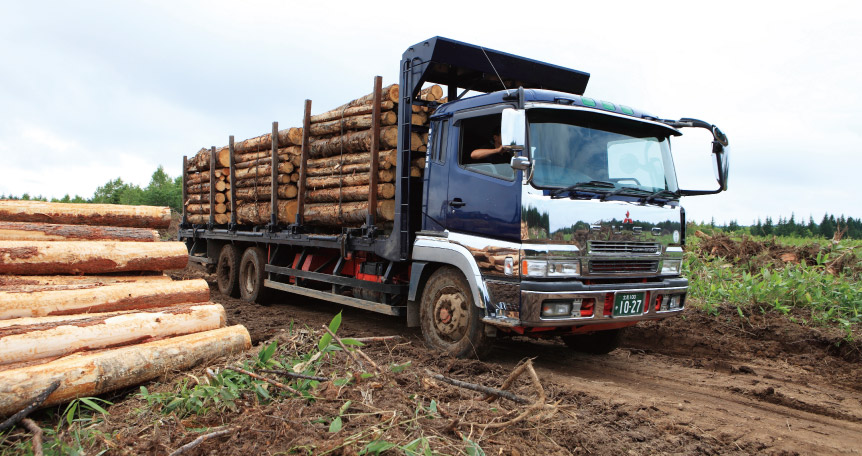
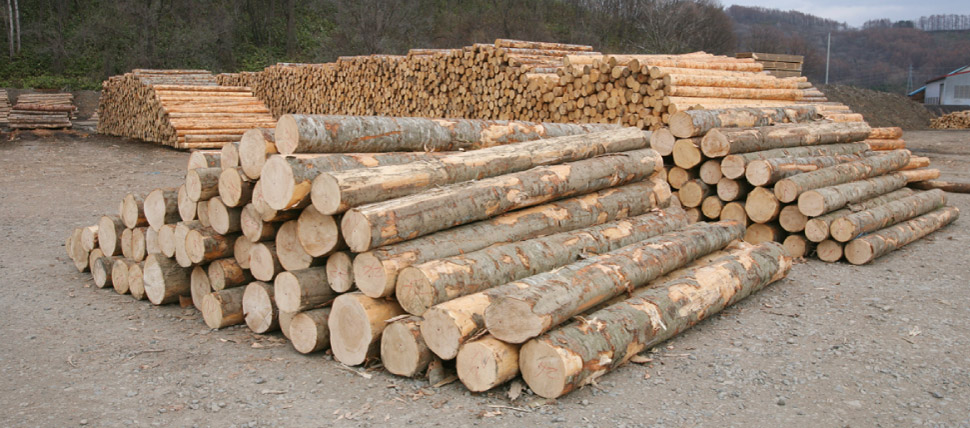
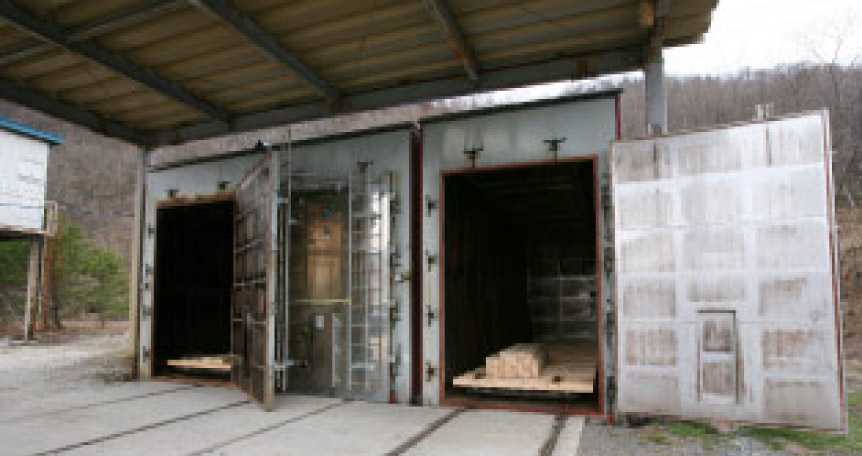
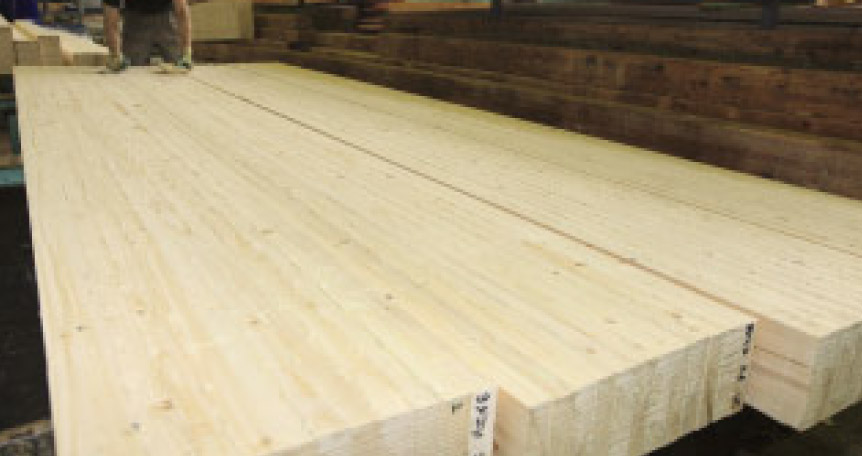
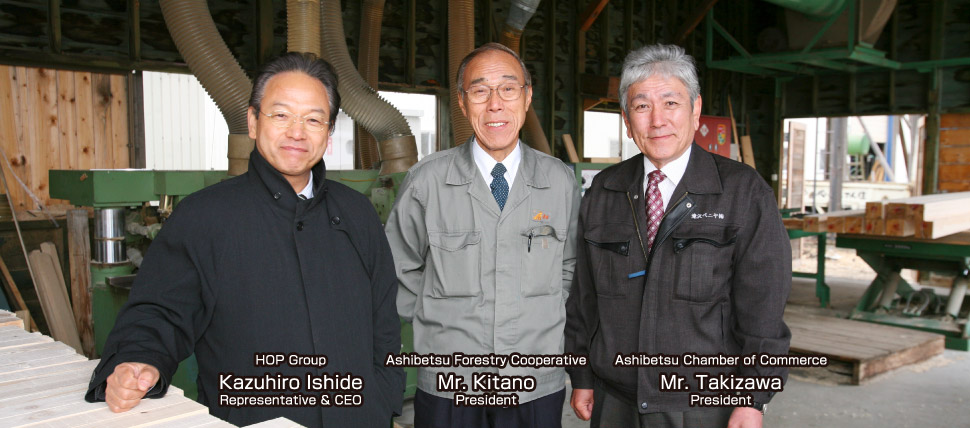
Significance of the active use of locally accredited certified forest timbers
Today, various forest certification systems have been launched across the world. These systems aim to protect and nurture their local forests by evaluating and certifying lumbers logged from appropriately managed forests based on a certain set of criteria and labelling them as certified products. In Japan, SGEC “Sustainable Green Ecosystem” Council led the commencement of the forest certification system in 2003.
For the past several decades, cheap imported lumber flooded the domestic market, causing the domestic forestry to recede, devasting forests, and leaving a tremendous damage on all industries surrounding forestry in Japan. In addressing the problem and revitalizing domestic forestry, sustainable management of forests is essential. The Forest Certification System by SGEC ensures such appropriate management of forests through evaluation and certification.
The system identifies the origin of the lumber and ensures consumer security through houses built with certified forest timber. In response to the initiative, HOP became one of the first companies to obtain SGEC forest certification. We will continue our effort to build more houses utilizing lumber produced in Hokkaido.
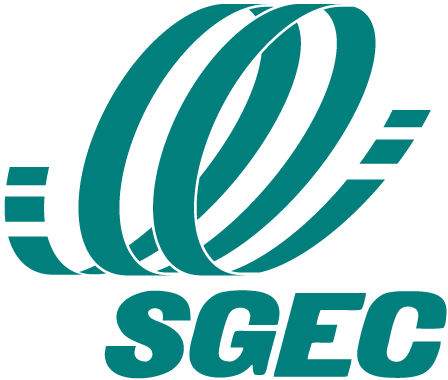
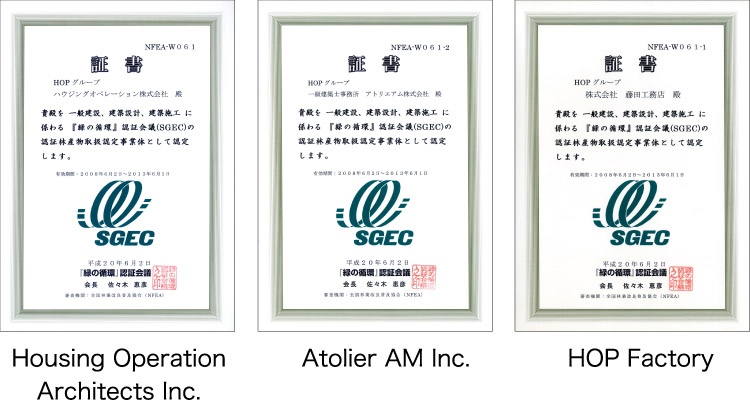
About SGEC “Sustainable Green Ecosystem” Certification
Forest certification systems were born in response to the radical destruction of tropical forests in the 1980s as a structure to guarantee “lumber produced from a sustainable forest management scheme”. In Japan, the Sustainable Green Ecosystem Council (SGEC) was launched at the inaugural general meeting by cofounders in June 2003, which incorporates the specific conditions of Japan with the globally recommended sustainable forestry standards.
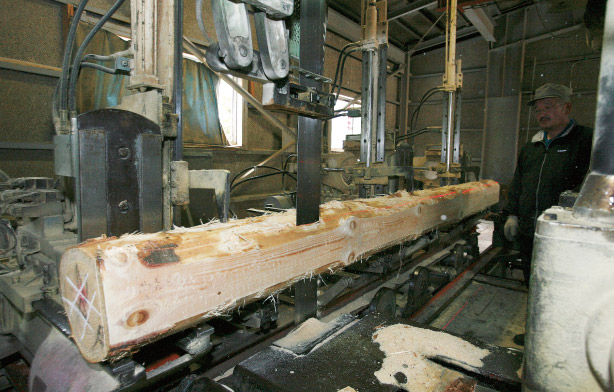
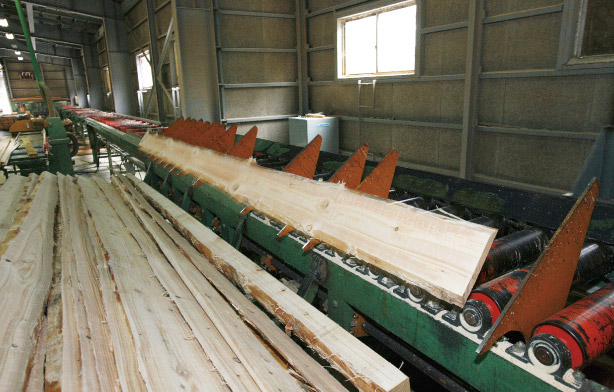
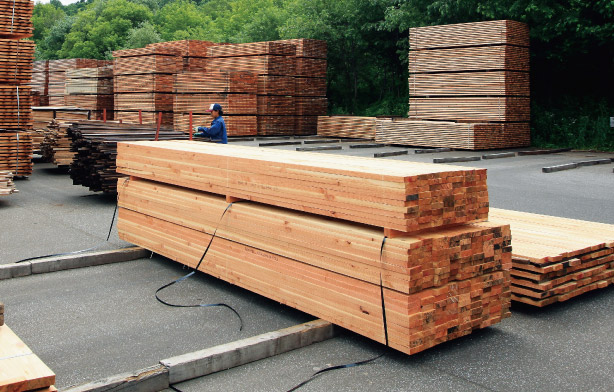
Lumbered raw wood are dried in a special drying house. The drying process is crucial in determining the quality of the products. At HOP, we select different optimum methods for structural members and fixture materials and adopt original drying method based on our extensive experiences and data.
We use sawdust and woodchips generated in the process of lumbering as the fuel for the drying house in an effort to minimize the use of fossil fuel and CO2 emission.
HOP Group Rubeshibe Plant develops and produces processed lumber made of thin slices of wood materials stuck together and boards made of woodchips glued together in a computerized cutting-edge facility. They are generally known as laminated timbers but also referred to as “engineering wood” because of their strength, which is about 1.5 times tougher than natural lumber, as well as their higher resilience against twist, warpage, crack, deformation, etc. Because these types of materials fully utilize residual and discarded wood, they also help our effort for the maximum use of resources.
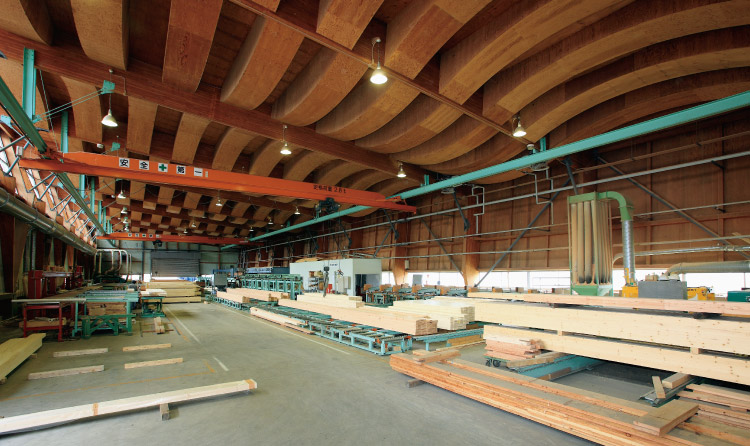
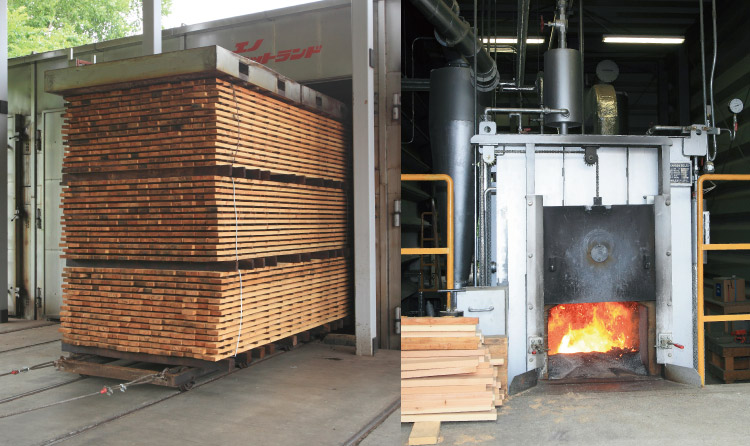
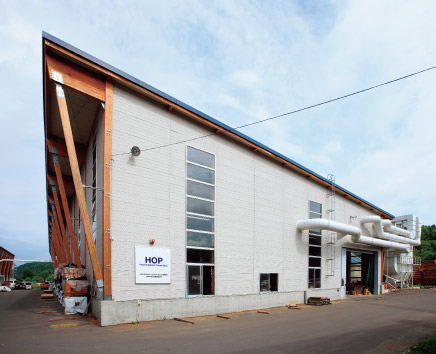
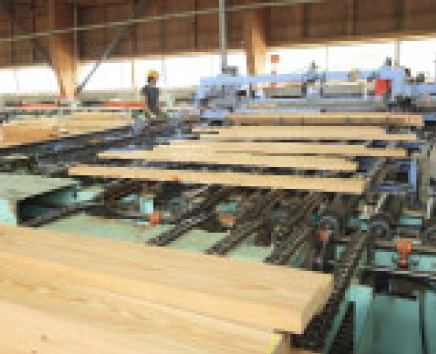
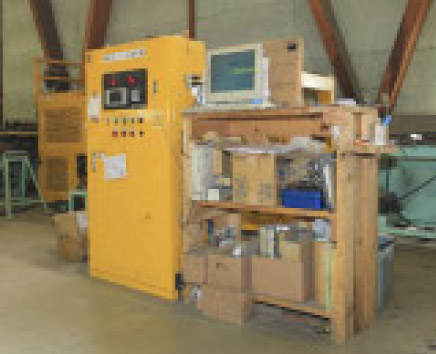
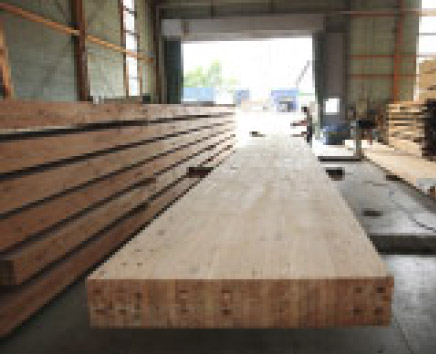
4-side slit method
HOP has developed the “4-side slit method”, a patented wood drying process technology enabling the direct use of thinned wood from artificial forests as pillars for wooden houses.
In this patented technology, thinned wood containing cores are shaped into pillars, on which grooves (slits) with a fixed depth are added from four sides and are dried at a lower temperature. The technology allows maximum utilization of a thinned wood.
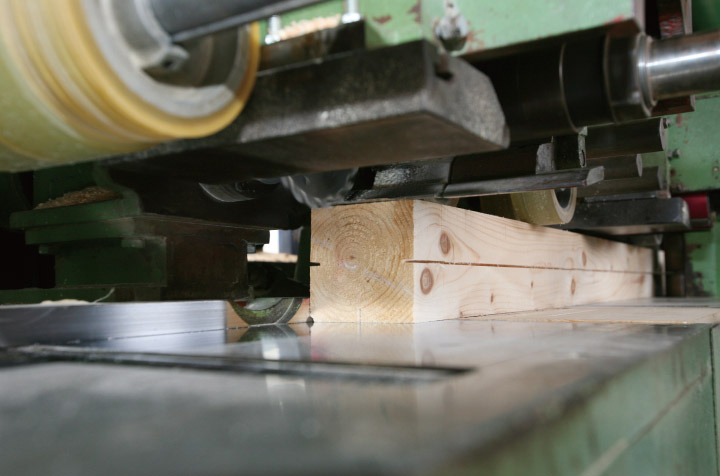
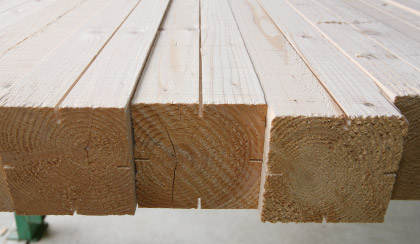
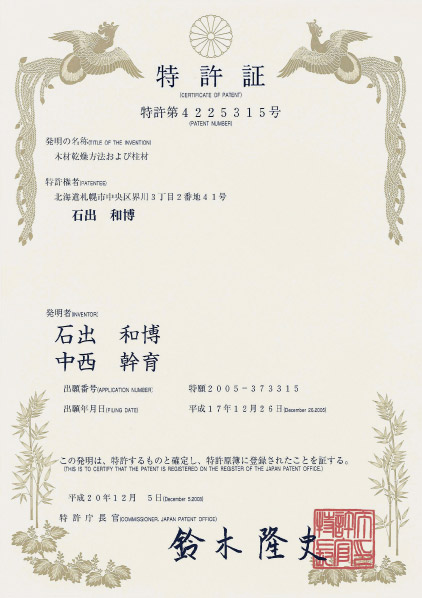
The precutting system, coordinated with the drawing, processes structural members with accuracy and speed
The computerized precutting system at HOP Precutting Plant adds joints and other processes to lumbered beams, pillars, and other structural members.
Complete structural members are promptly sent to their designated construction sites to ensure smooth completion of framework within a short time span.
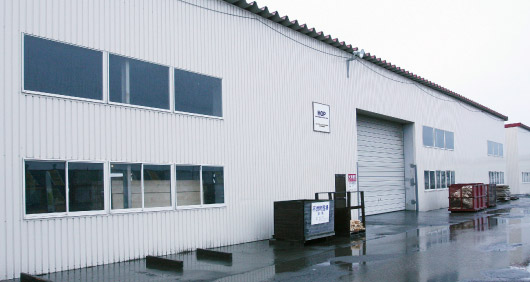
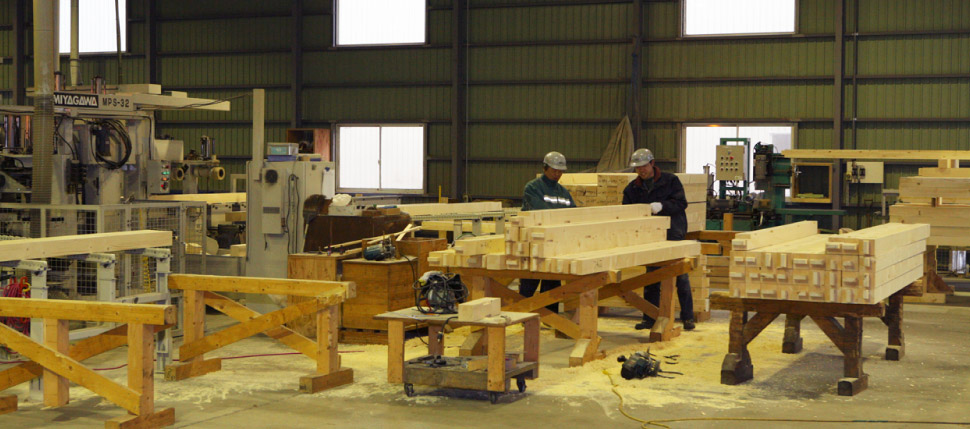
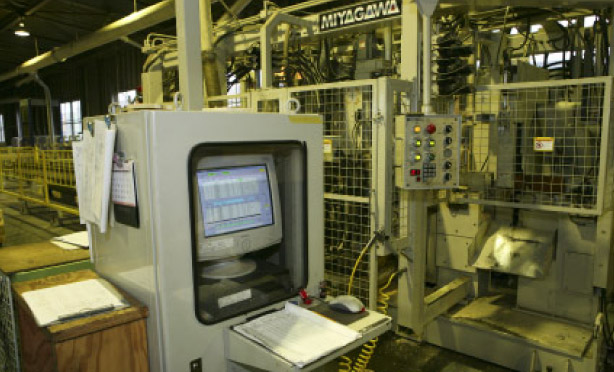
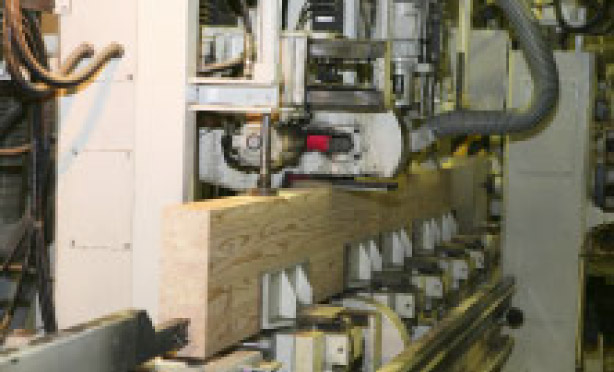
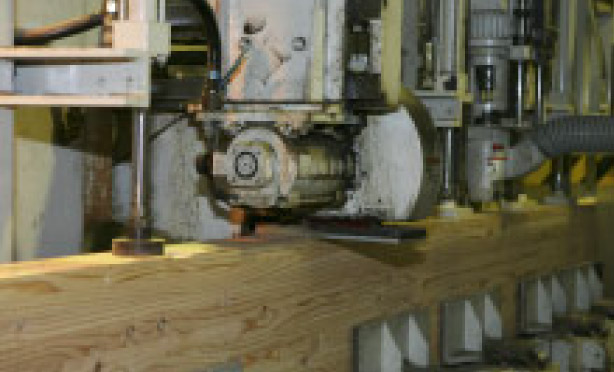
CAD data is based on the design drawing prepared by HOP.
Computerized processing based on the drawing enables the steady production of highly uniform housing components.
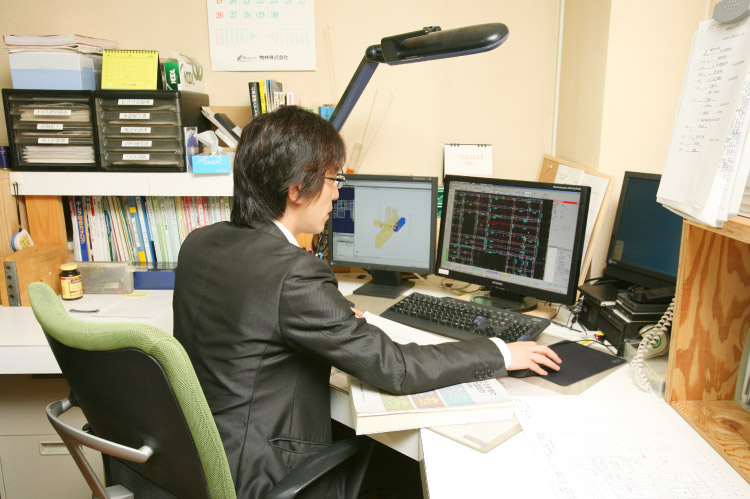
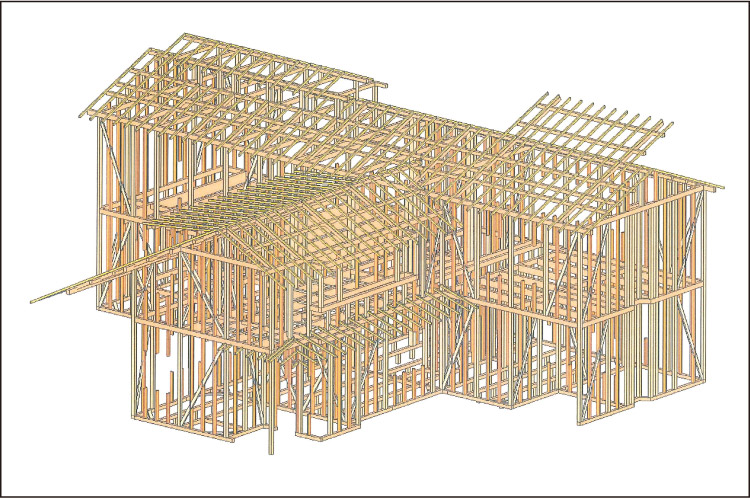
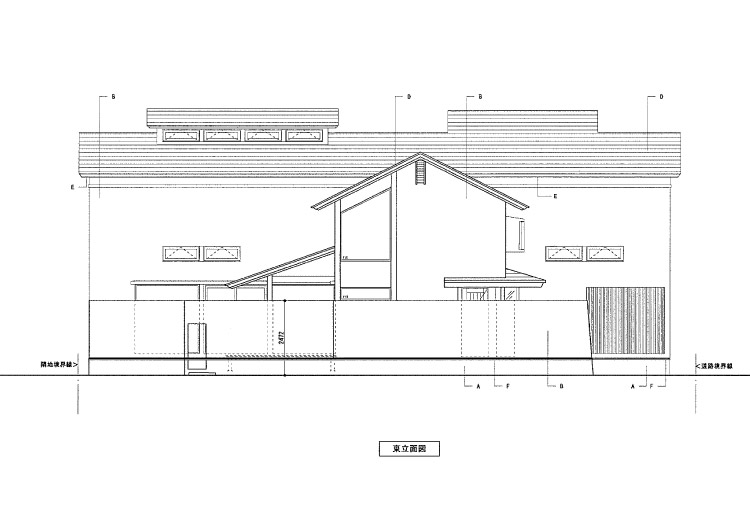
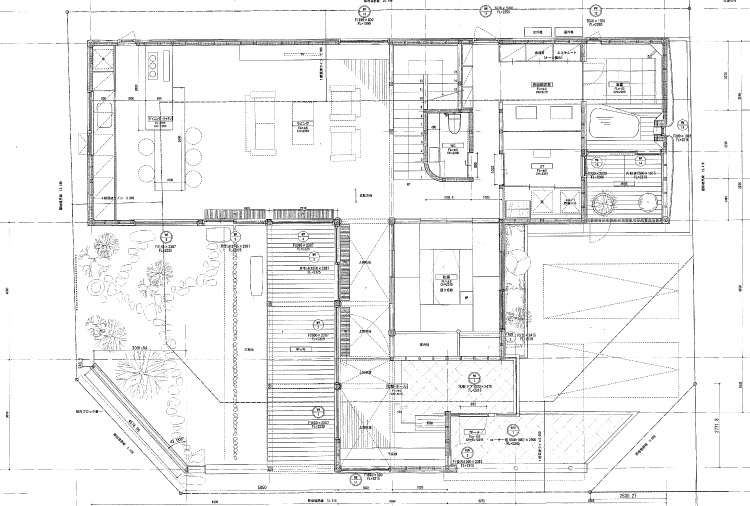
HOP design drawing. Floor plan (right) and elevation plan (left)
Assembly at each construction site
Structural members directly delivered from the Precutting Plant are assembled on the site.
The joints used to assemble different components are HOP’s patented original hardware. 2.5 times stronger than other existing products, the hardware guarantee a robust building frame.
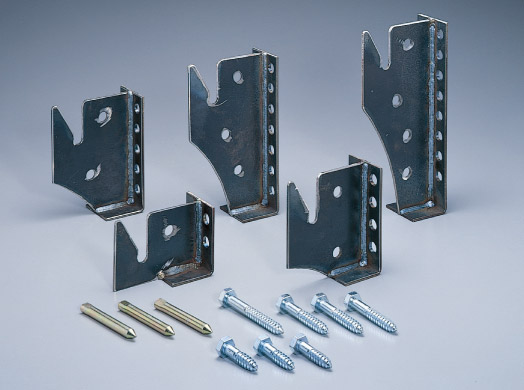
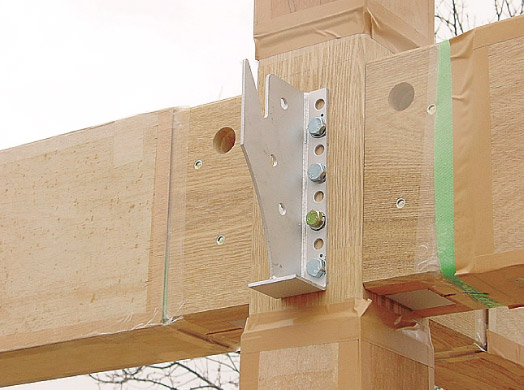
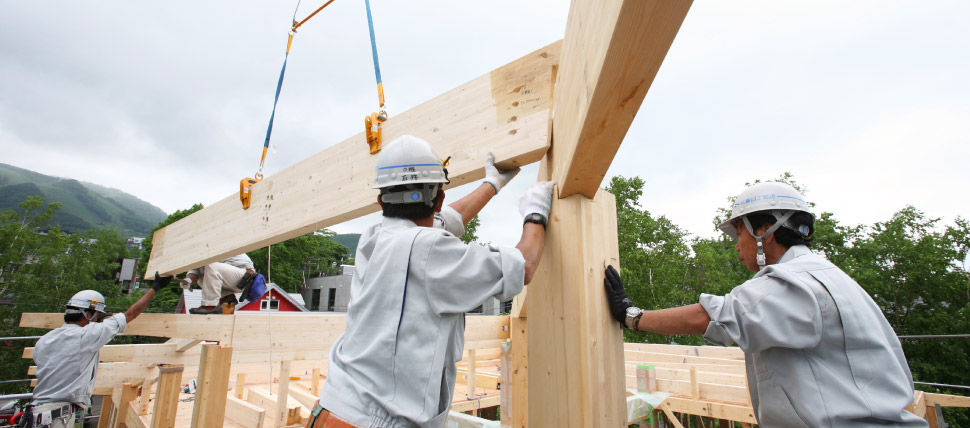
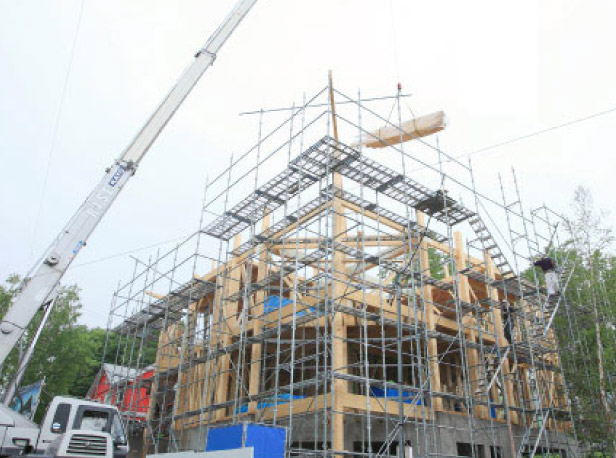
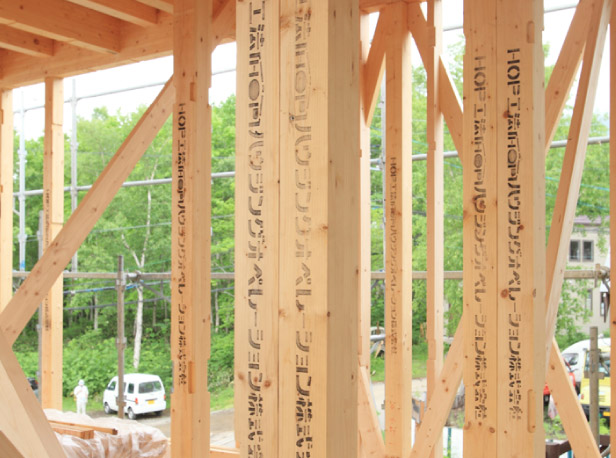
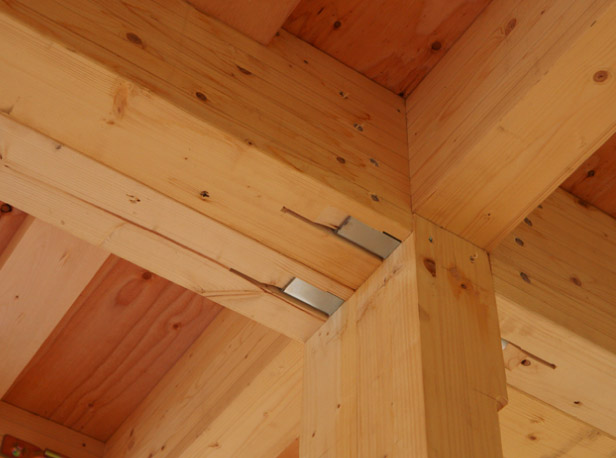
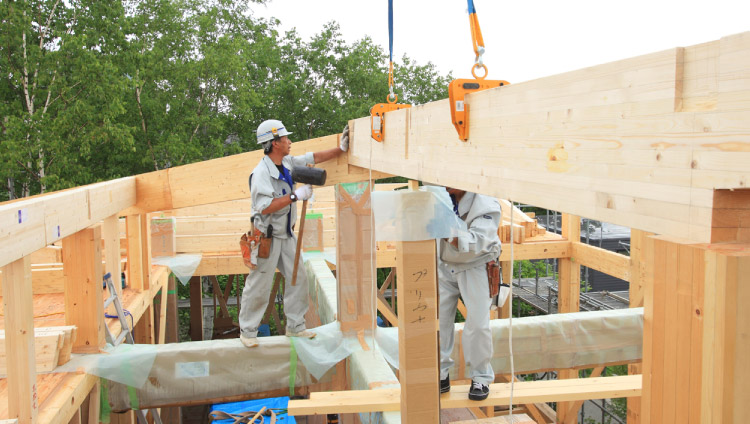
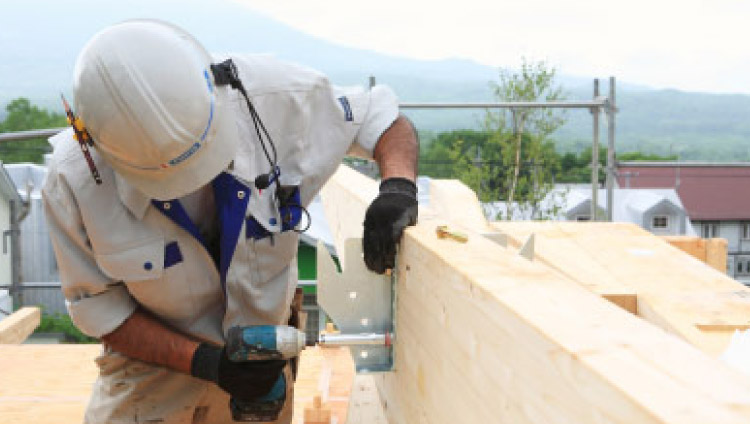
All furniture and joineries are made in the company’s factory
In order to meticulously respond to specific orders, such as joineries, furniture, staircase material, baseboard material, etc. with a millimeter precision, fitted furniture are also manufactured at the company’s Okadama Plant. We do not resort to readymade joineries because we are obsessed with quality with a higher accuracy. We use natural woods like tamo, water oak, castor aralia, Japanese cypress, cedar, and pine tree for interior. HOP’s houses embody the architects’ commitment to the clients’ happiness and craftsmen’s professional pride.
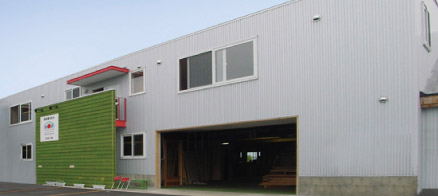
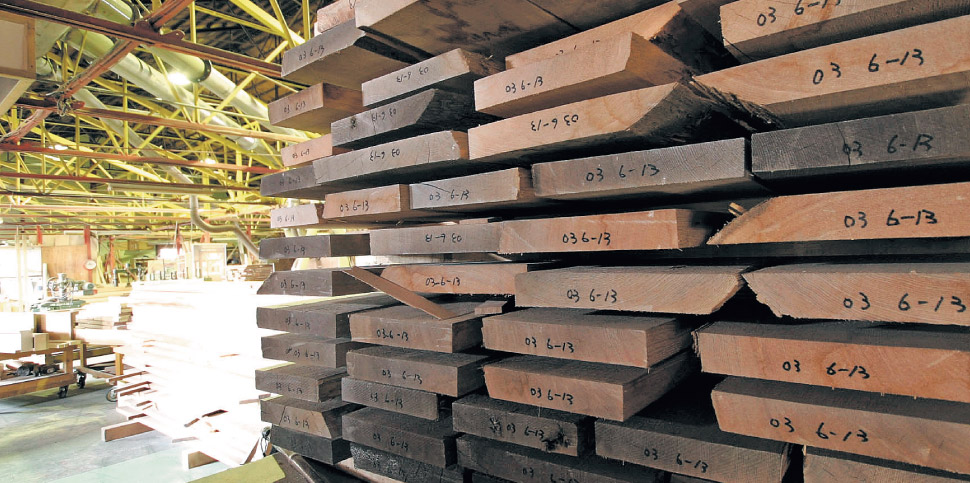
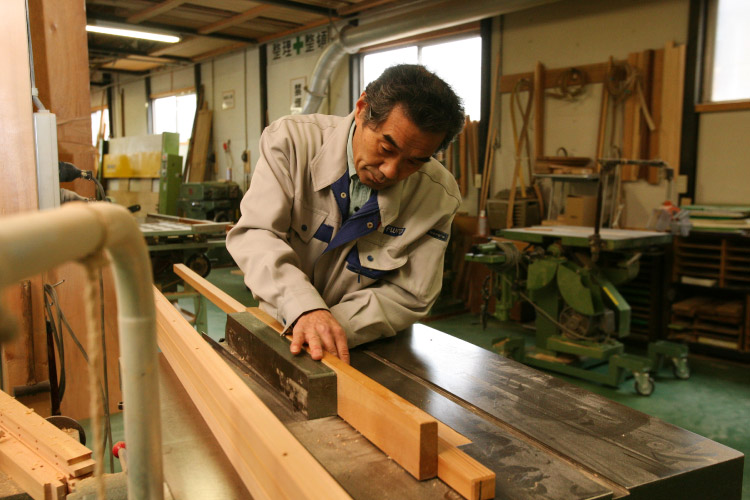
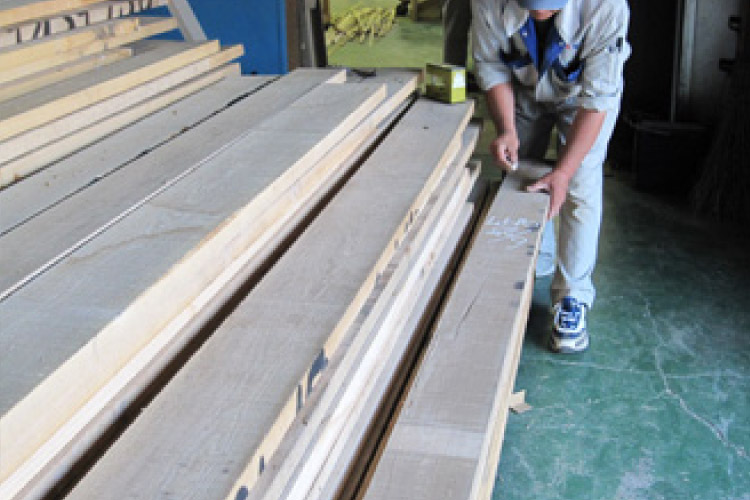
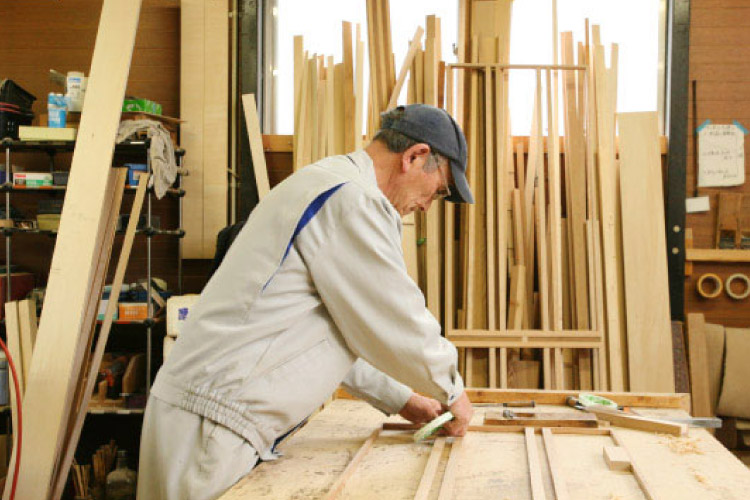
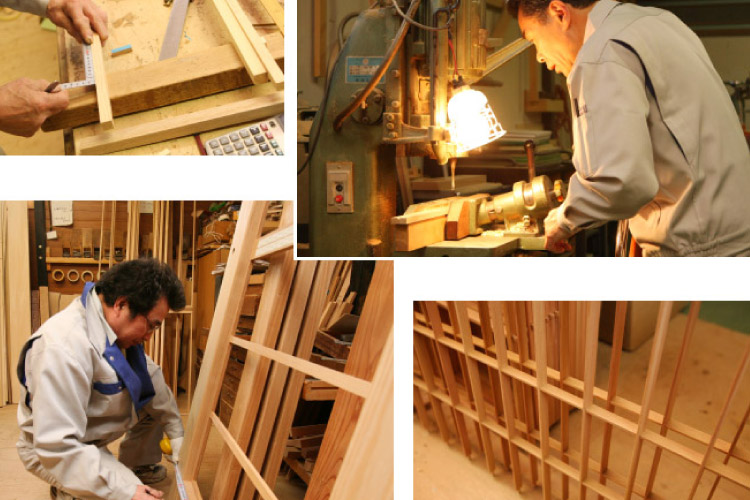
Fitting
Components produced at the plant are brought to the construction site, where they are fitted to the building.
Quality furniture and joineries define the dignity of each house, which the residents lovingly look after for many years.
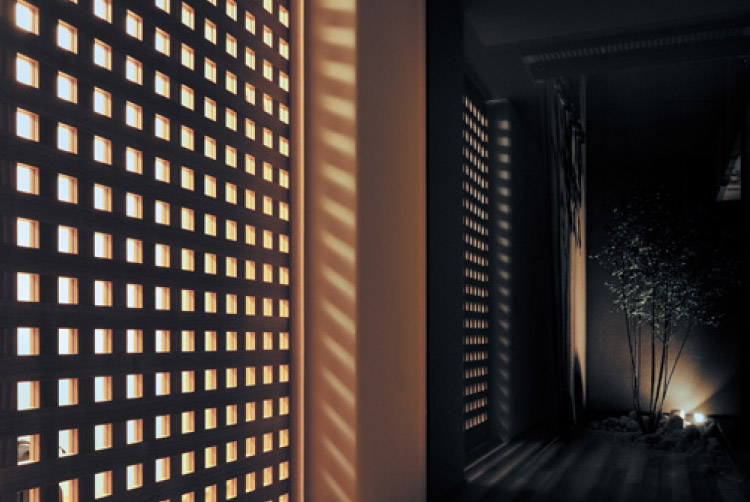
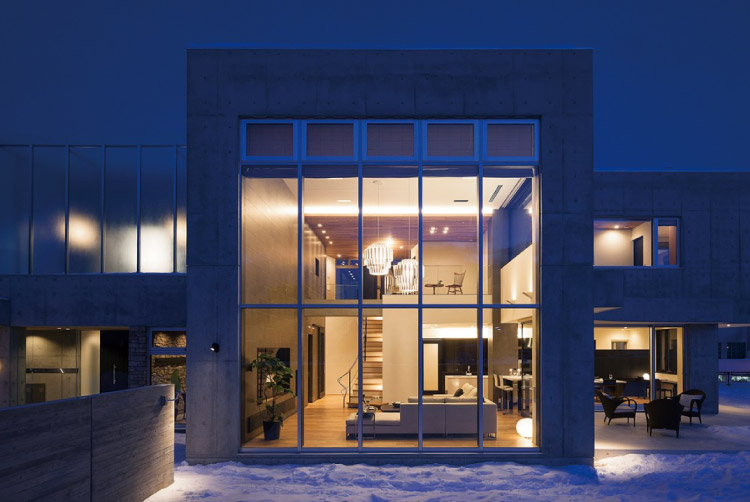
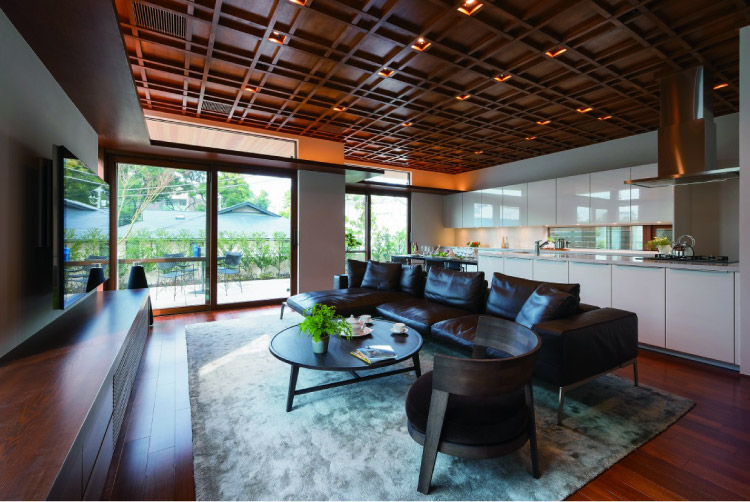
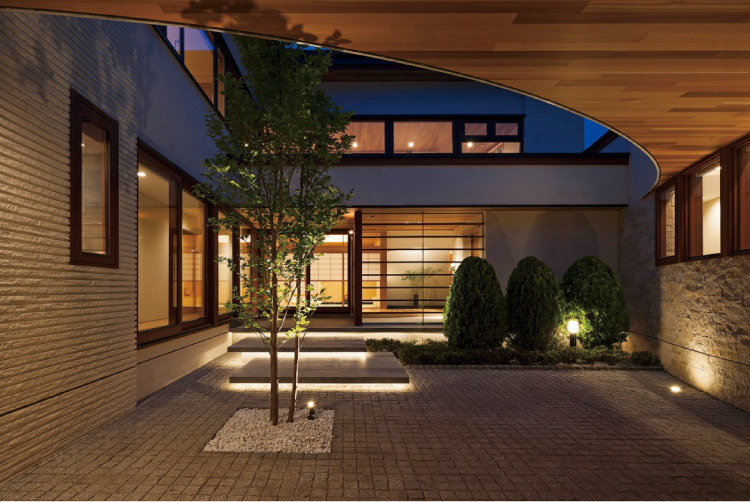